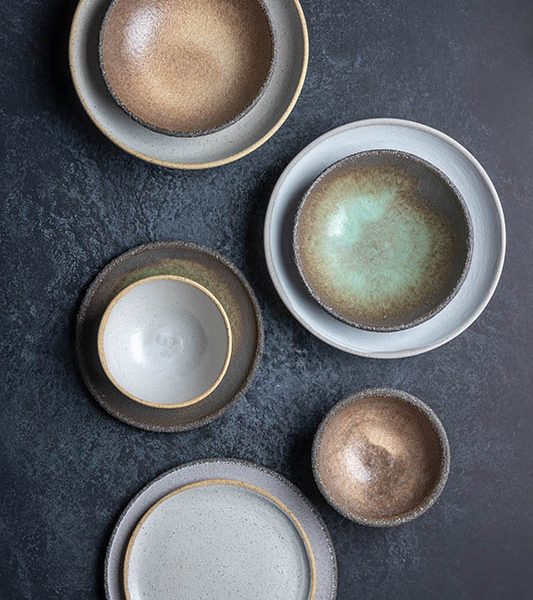
About production
The production process is the most important and the most difficult part of our work. It is time-consuming and requires many steps to complete. The main feature is the detail in everything. There are many details, which must be followed faithfully every time on every ceramic object, so that the result is perfect and as similar as possible every day. This is perhaps the greatest difficulty that makes ceramics. One wrong move or one wrong step can be fatal. The aim of this text is to inform you about the ceramics we stand for.
The production methods we use at Dipno are the following:
- Cast moulds
- Wheel
- Cutthroat
- Rotary press
- Hydraulic press
For cast moulds the procedure is as follows.
We make the mould ourselves, which consists of plaster. The mould is filled with cast clay (Casting Slip), remains in the mould for a period of time and then emptied as we wait for it to dry. The next day we open the mould, remove the object from inside and proceed to the point of final shaping while it is still wet.
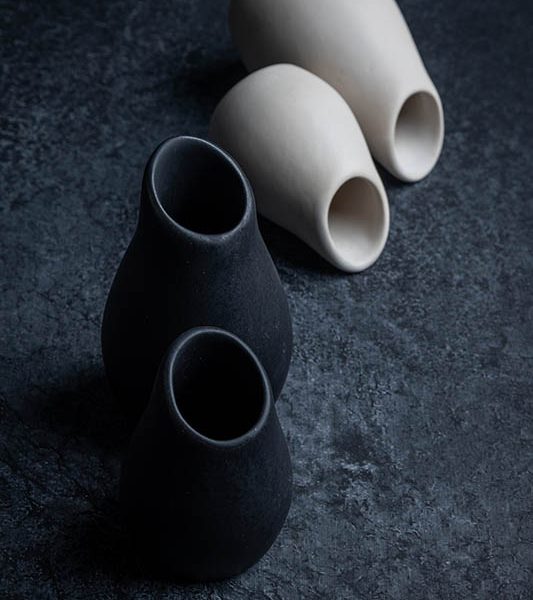
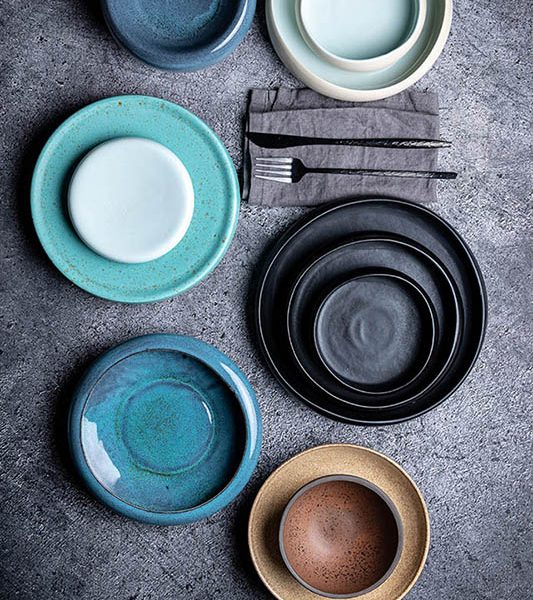
For the wheel the procedure is as follows:
Here we use masses of ceramics (Clay bodies) which we work by hand (kneading) to remove any air that may be present inside and create the so-called shells so that we can transfer them to the wheel and create the object by hand.
For the cutthroat the process is as follows:
Here we use ceramic masses (Clay bodies) which we work by hand (kneading) to remove any air that may be present inside, we divide the clay into parts, we place the mould in the lathe, we fill it with the clay and with the help of each knife we give it its final form.
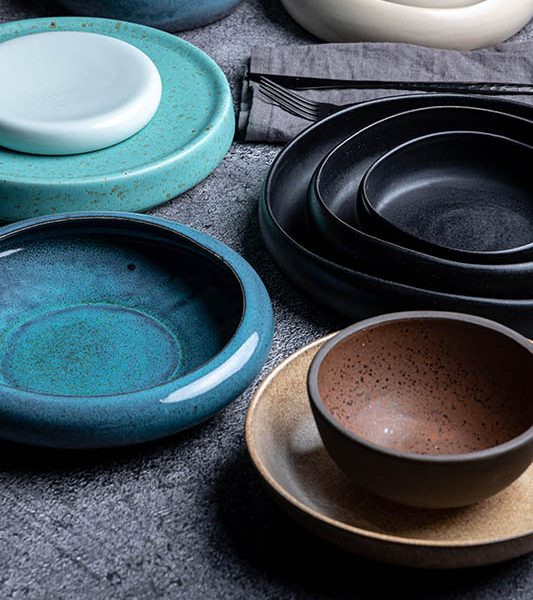
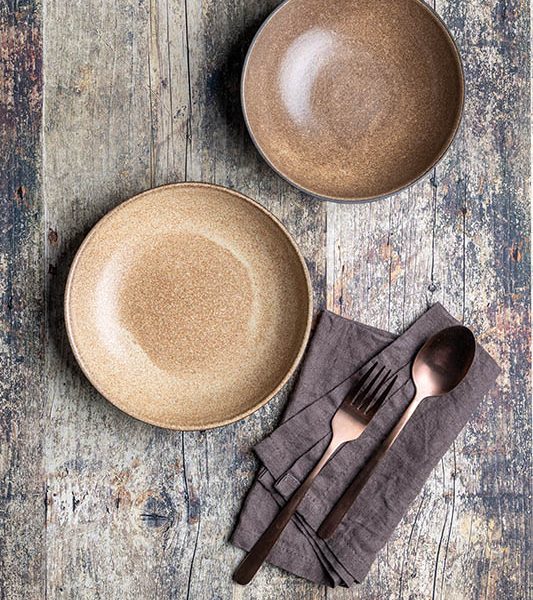
For the rotary and hydraulic press the procedure is as follows:
We use metal or plaster moulds (which we make ourselves) and by using a male-female mould and high pressure we shape the clay according to the mould.
The next steps are the same for all modes of production. First we let the ceramics dry, followed by scraping and mopping to make the final finish.
This is followed by the 1st bake (biscuit) to give the ceramic a typical hardness so that we can polish it (painting).
After glazing follows the 2nd and last bake so that the object is ready for use.
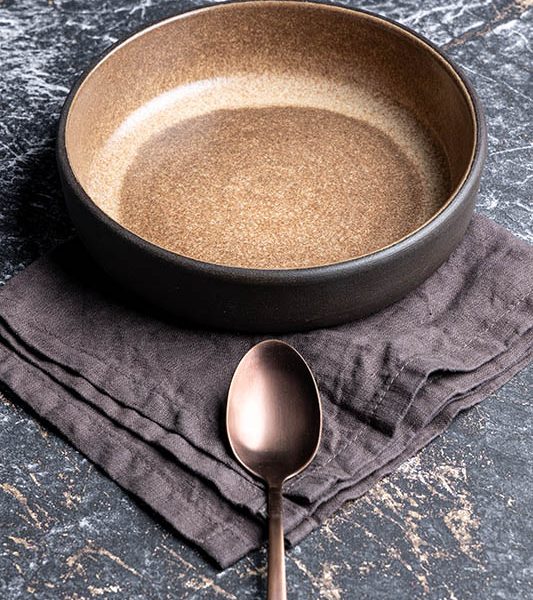